Infrastructure
At the heart of every successful packaging enterprise lies a robust infrastructure that seamlessly integrates technology, expertise, and innovation. Welcome to Printmann Packaging, where we take pride in our state-of-the-art infrastructure designed to deliver unparalleled packaging solutions to our clients worldwide.
Central to our infrastructure is our advanced manufacturing setup, where precision meets efficiency. Our production lines are optimized for flexibility and scalability, allowing us to cater to both large-scale production runs and bespoke packaging solutions with equal ease. From automated packaging machinery to specialized equipment for custom requirements, our manufacturing capabilities are second to none.
WORKFLOW:
We Printmann Packaging make sure the process of working in box manufacturing follow all the key
steps, from design to
delivery. Here’s an overview of the typical workflow :
1
Client Consultation and Design
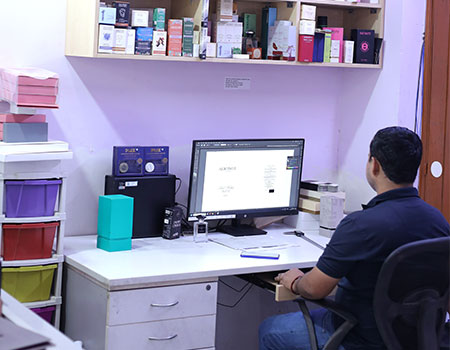
- Initial Consultation: Understand the client's needs, including box type, dimensions, materials, and design preferences.
- Concept Development: Work with the client to develop concepts and prototypes, incorporating branding elements and specific requirements.
- Design Approval: Create detailed design mockups and samples for client approval.
2
Material Selection
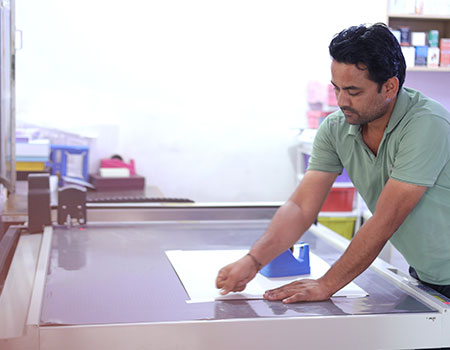
- Material Options: Choose appropriate materials based on the box’s intended use, such as cardboard, corrugated board, or specialty papers.
- Quality Assurance: Ensure materials meet required standards for durability, printability, and environmental impact.
3
Prototype Development
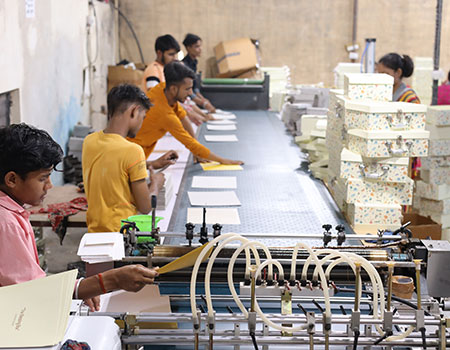
- Sample Creation: Develop prototypes or sample boxes to test the design and functionality.
- Client Feedback: Obtain client feedback on the prototypes and make necessary adjustments.
4
Pre-Production
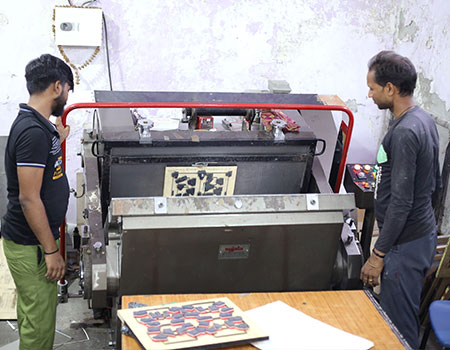
- Tooling Setup: Prepare and set up the necessary tooling, such as dies and molds, for mass production.
- Print Preparation: Prepare printing plates and artwork for branding and design elements.
- Pre-Production Testing: Conduct tests to ensure all equipment and materials are ready for full-scale production.
5
Production
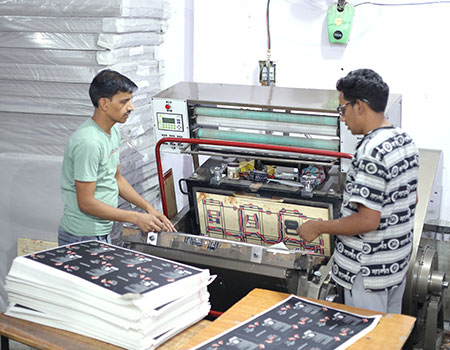
- Cutting and Scoring: Cut and score the cardboard or other materials to create the box’s shape.
- Printing: Apply designs, logos, and other graphics using various printing methods, such as offset or digital printing.
- Folding and Gluing: Fold and glue the printed sheets to form the final box structure.
- Quality Control: Inspect each box for defects, ensuring that they meet quality standards and client specifications.
6
Finishing Touches
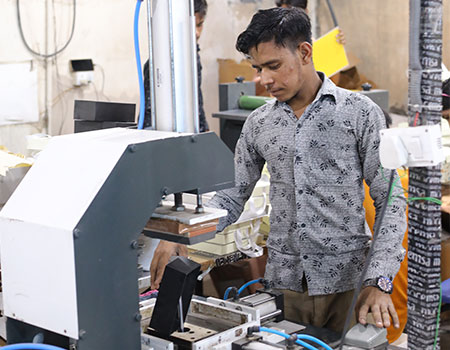
- Additional Features: Add any additional features such as embossing, foil stamping, or custom inserts if required.
- Packaging: Package the finished boxes securely to prevent damage during transportation.
7
Delivery and Logistics
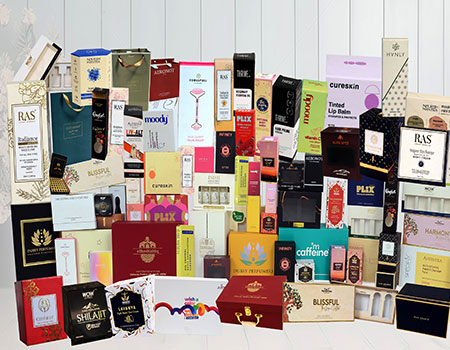
- Order Fulfillment: Coordinate the logistics for shipping and delivery according to the client's requirements.
- Delivery Tracking: Provide clients with tracking information and handle any issues that arise during delivery.
8
Post-Production Support
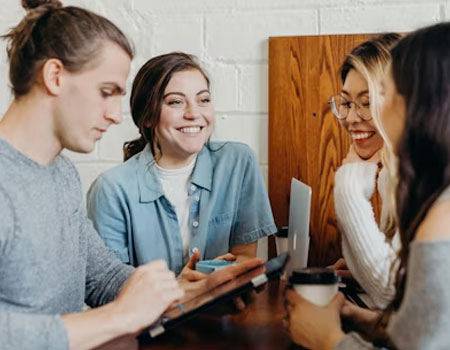
- Client Feedback: Gather feedback from the client to address any concerns and improve future processes.
- Reorders and Adjustments: Manage reorders and make adjustments based on client needs and market trends. Key Considerations Throughout the Process
- Sustainability: Focus on using eco-friendly materials and practices where possible.
- Cost Efficiency: Balance cost with quality to provide value to clients.
- Lead Times: Manage production schedules to meet client deadlines.